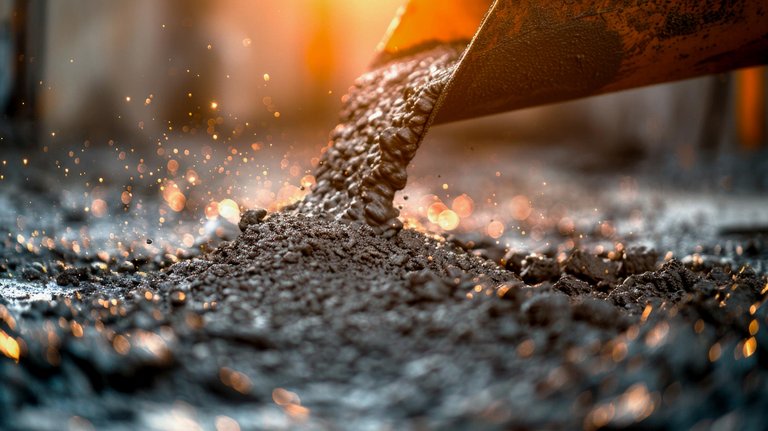
Recycling a mountain of concrete waste
Every year, a total of 500 million cubic meters of fresh concrete is discarded1. Sika has developed an innovative solution to recycle this valuable construction material and make it ready for reuse.
The construction industry is under increasing pressure to address two key challenges: reducing carbon emissions in line with the Paris Agreement, and moving away from a linear to a circular economy to improve resource efficiency. For the concrete industry, this means lowering clinker content in cement to cut emissions, and increasing concrete recycling to support circular practices.
Globally, 4% of the fresh concrete is returned to the factory unused for several reasons2. A surplus is often deliberately planned in order to avoid material bottlenecks. Delays on the construction site, last-minute cancellations, mixing errors, and quality problems also lead to fresh concrete remaining unused.
4% of fresh concrete is returned unused to the plant, without being further utilized.
Most of this concrete waste ends up in landfills.
The vast majority of this unused concrete ends up in landfills. Only a small proportion is used for building roads or is processed into concrete Lego-like bricks for walls or retaining walls. But ultimately this leads to “downcycling” – the conversion of high-grade construction material into an end product with inferior properties. While the amount of unused concrete from individual construction sites may seem manageable, when viewed as a whole it adds up to a global mountain weighing in at around 500 million cubic meters annually.
CONCRETE RECYCLING HAS MANY BENEFITS
This towering waste could be avoided if the material is reused. Sika has developed solutions that allow for concrete plants to recycle returns. The Sika solutions create an aggregate that can be reintroduced into the production cycle. In addition, when a concrete truck is left with more than half a cubic meter of unused material, it often has to make a detour to a waste management facility. Sika's innovative solution eliminates the need for extra trips, allowing trucks to return much faster.
Moreover, it helps plants to meet their carbon emissions reduction targets. For every cubic meter of concrete produced, around 200 to 400 kilograms of CO2 emissions are released3. “Recycling even a fraction of the returned concrete would save vast amounts of CO2,” says Chachi Tilocca, National Sales Manager Concrete at Sika Australia.
“Recycling even a fraction of the returned concrete would save vast amounts of CO2”
National Sales Manager Concrete at Sika Australia
FROM FRESH CONCRETE TO DRY GRANULATE
Sika’s solution for recycling unused concrete is based on a simple principle. When trucks arrive at the plant with leftover concrete, the driver or concrete operations manager adds a powder-based additive directly into the mixer drum. This removes moisture from the concrete after a short mixing time in the truck, and the resulting mix is a dry granulate. “It’s quite easy to hear the consistency of the material transforming from the sounds coming from the drum,” explains Mark Benes, Target Market Manager Concrete at Sika Australia.
Within three minutes, the material emerges from the mixer drum in the form of aggregates. “The recycled concrete is then ready for reuse, either as aggregate in new concrete or for the substructure of new roads,” explains Mark. When making fresh concrete, factories can replace 20 percent of the gravel component with this granulate. Sika’s admixture products are user-friendly, as they do not require specific infrastructure or employee training.
The solution
The driver simply adds one bag of Sika admixture per cubic meter.
This removes moisture from the concrete after a short mixing time in the truck.
The granulate needs to be loosened up by driving over it once or twice. This allows the remaining moisture to evaporate.
100% of the resulted material can be reused – either as an aggregate in new concrete or for the substructure of new roads.
In concrete production, this recycled material can replace up to 20% of the gravel.
Benefits
Easy to use without the need for any additional equipment leaving the mixer drum clean.
“It’s quite easy to hear the consistency of the material transforming from the sounds coming from the drum”
Target Market Manager Concrete at Sika Australia
DEMAND FOR CONCRETE RECYCLING ON THE RISE
Sika currently offers its innovative admixtures to the USA, Canada, Australia, New Zealand, Brazil, Chile, and Mexico. “Customer feedback is extremely positive,” says Chachi. “The factories are interested in concrete recycling, partly for costing purposes, but also because of increasingly stringent regulations, and the move towards a circular economy.” He also points out that the demand for recycled concrete is growing in the market. “Many projects for the public sector now stipulate a minimum amount of recycled concrete.”
As this trend is expected to continue, Sika intends to introduce these technologies in other countries in the coming years. With this initiative, the company is enabling the construction industry to improve its environmental footprint, and supports the global efforts to reduce concrete waste, by keeping valuable raw materials in circulation.